Your exchangers manufacturer
The heat exchanger is an equipment that has been manufactured by Labbe Process Equipment for more than 70 years.
The range of heat exchangers offered by Labbe Process Equipment is complete with:
Stainless Steel or Nickel Alloys Tubular heat exchanger : Tubulex
Wide-channel welded plates heat exchanger : Weplex®
Heat exchangers with cylindrical shell : Compalex®
Finned tubes heat exchangers : Economizers – Ecofinex®
In addition, Labbe masters internally all the manufacturing phases to ensure quality work and the shortest delivery times.
Thanks to our experience, we are able to offer you the thermal and mechanical design of your heat exchanger. Indeed, we have an integrated design office.
What is an exchanger
An exchanger is an equipment allowing a heat transfer. This can be to cool, heat or condense a liquid. It is generally composed of a tubular bundle, a shell, tubular plates as well as distribution boxes.
Also, heat exchangers are regulated by the TEMA (Tubular Exchanger Manufacturer’s Association). This an association of manufacturers of tubular heat exchangers. TEMA has established a set of exchangers construction codes. These are regularly updated and published.
As a result, most of the heat exchangers used by the process industries are built to TEMA standards.
Conception and manufacturing of a heat exchanger
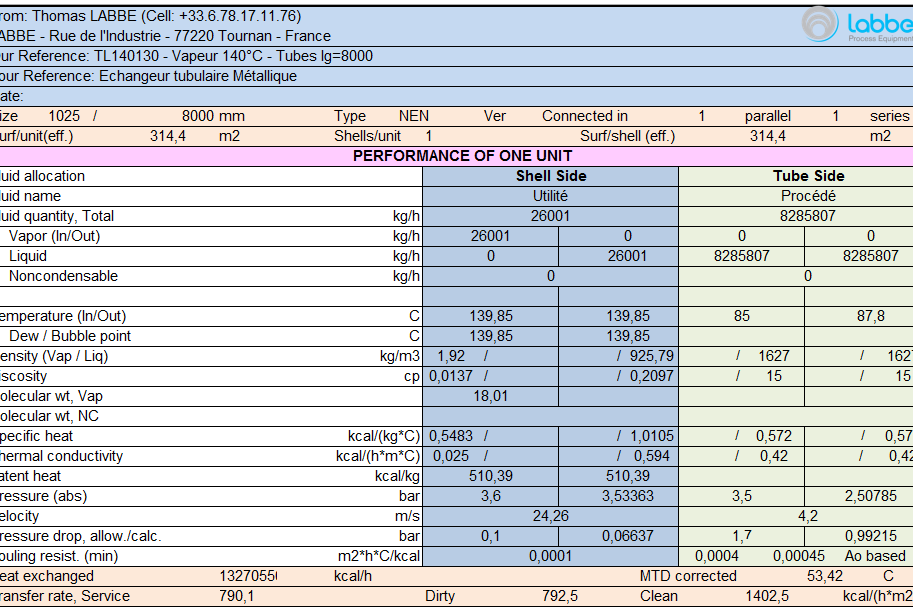
Step 1 : Thermal calculation
Labbe Process Equipment has know-how and long-standing experience, therefore we are able to define the type of exchanger suited to your needs. Also, we will define the power and the exchange surface. This is done according to your industrial process requirements (fluids, density, viscosity, use, operating conditions, etc.) but also in accordance with the TEMA construction standard.
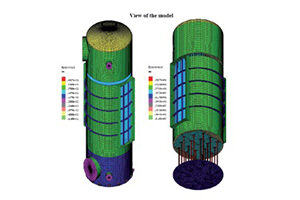
Step 2 : Mecanical calculation
Once the geometry of the heat exchanger has been defined, Labbe performs mechanical design calculations. Our goal is to determine the wall thickness of the calender, the thickness of the boxes as well as the thickness of the tube sheets. We also determine the need for an expansion bellows.
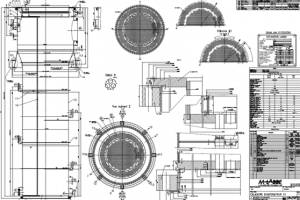
Step 3 : Manufacturing plans
Finally, with all the dimensions of the heat exchanger defined, we draw up the manufacturing plans. These contain details of the different parts of the heat exchanger.
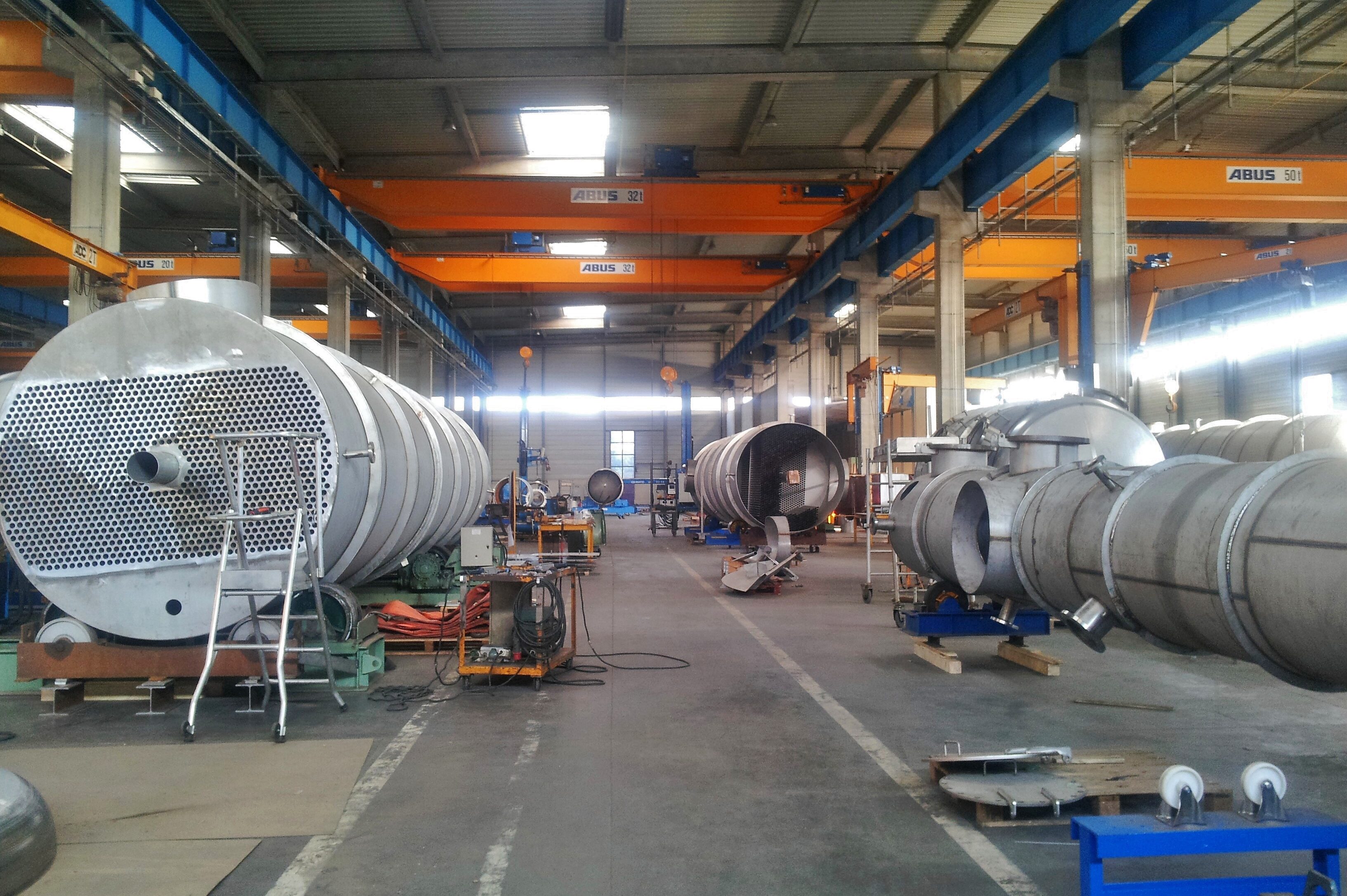
Step 4 : Manufacturing
Manufacturing steps of an exchanger made in our workshops:
1. Cutting of sheets
2. Forming dished heads
3. Machining of tube sheets, baffles and flanges
4. Rolling of the shells / production of the calender
5. Automatic welding for circular and longitudinal ones,
6. Manual welding for taps,
7. Tubing (welded and / or expanded tubes) / installation of plates
8. Polishing, pickling and passivation,
9. Regulatory tests
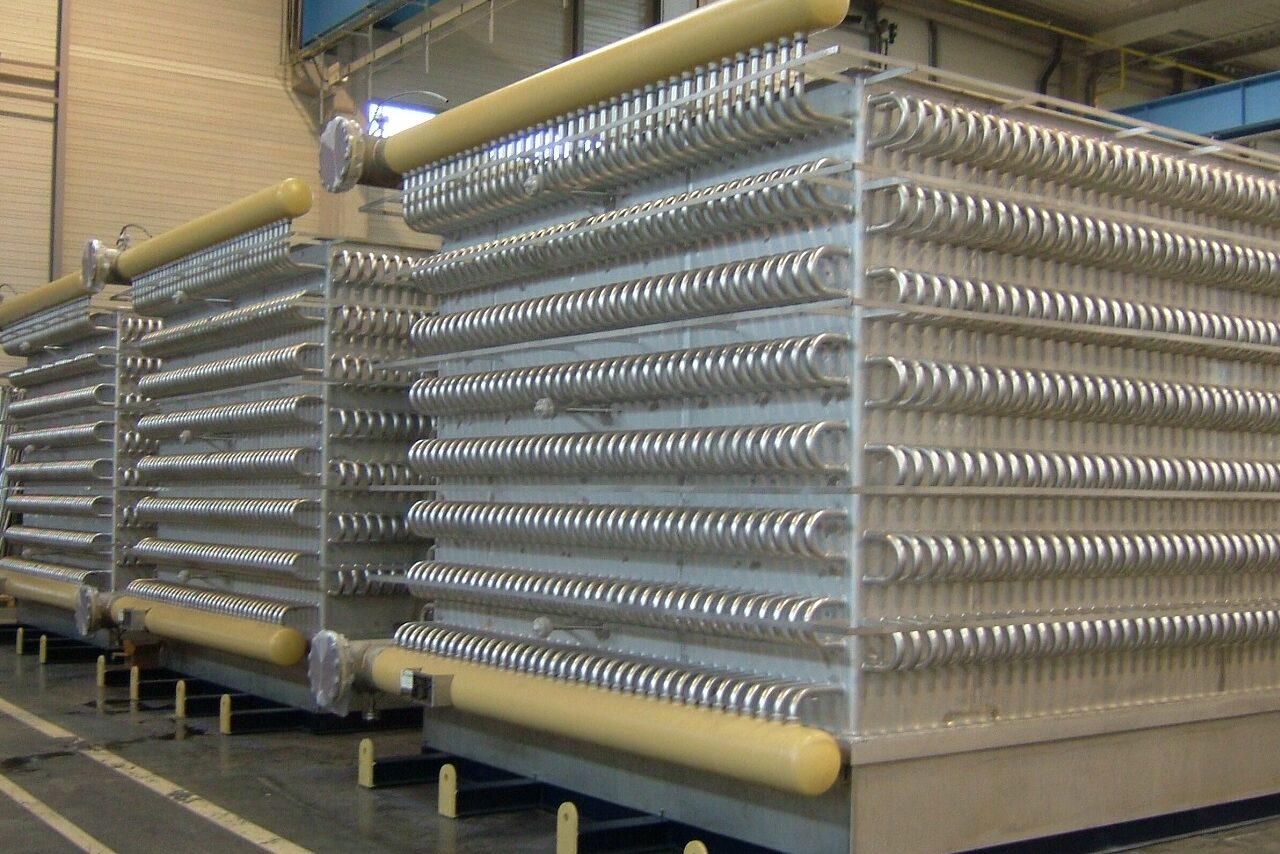
The different modes of heat transfer
This convection, corresponding to the transfer of thermal energy between two fluids through an exchange surface, can be carried out in several ways using devices:
– Co-current: the exchanger is crossed by the two fluids in the same direction.
– Against the currents: fluids flow through the device in the opposite direction.
– Cross current.
Heat exchangers can handle a multitude of different fluids.
The heat exchange can take place between:
– Gas / gas
– Liquid / gas
– Liquid / Liquid
– Condensation
– Evaporation
– Air / water
Materials used in the manufacture of exchangers
– Stainless steel 304L, 316L, 316Ti, 321, 310S
– Duplex U45N, U35N
– Uranus B6
– Nickel alloys C22, C276, C2000
– Incoloy
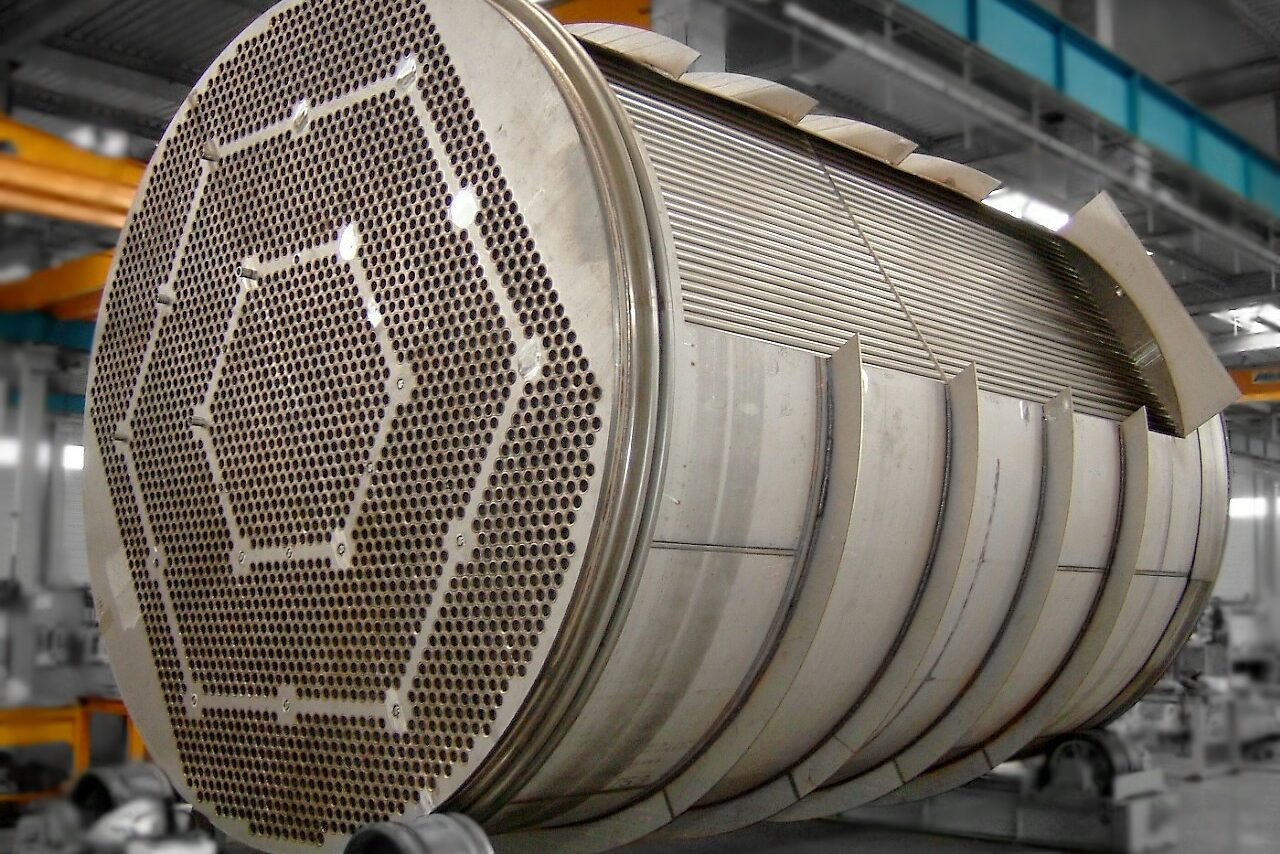
Differents types of heat exchangers
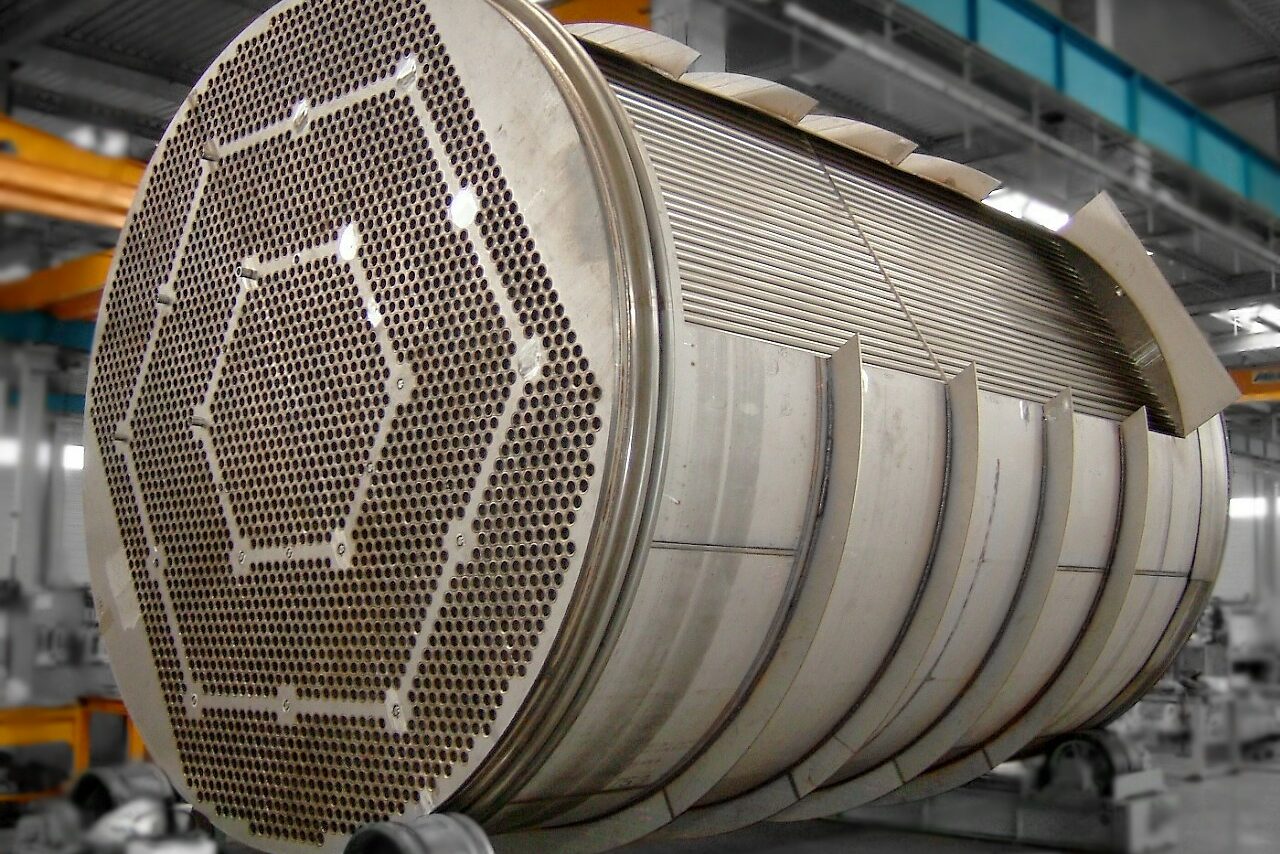
Shell and tubes heat exchangers

Finned tubes exchangers
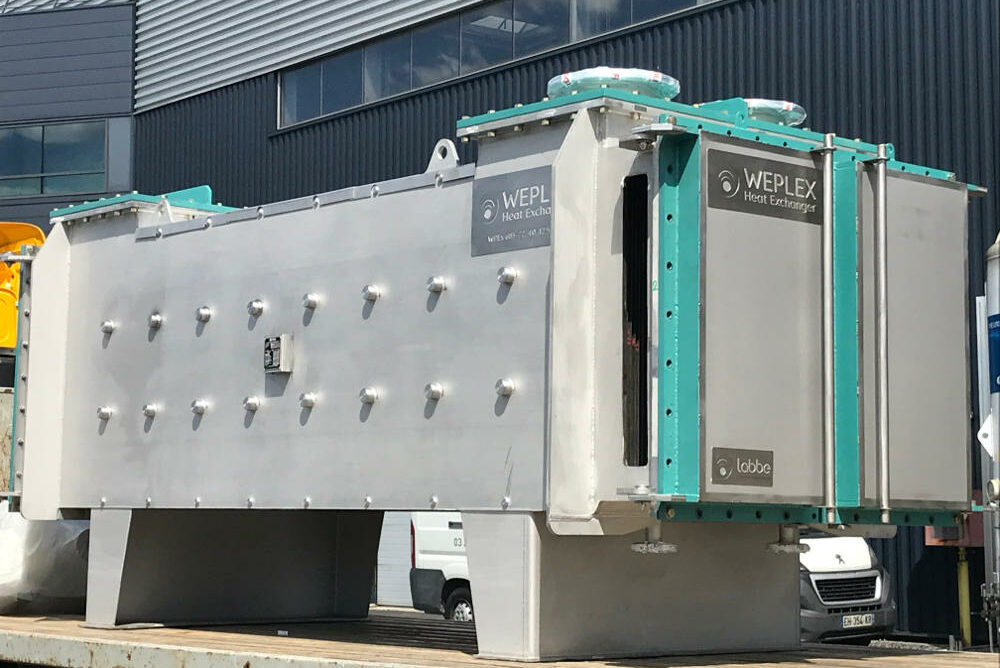
Welded plates heat exchanger
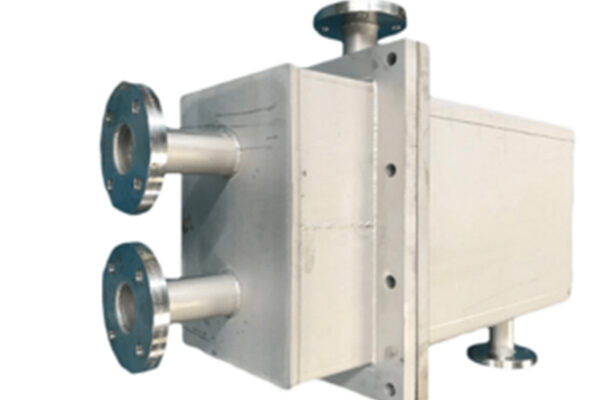